EPRI Pursues Broad Portfolio of Efficient Plant Cooling Technologies
In 2015’s record heat, drought across the Western United States ranged from severe to exceptional, creating hardship and danger from California to the typically wet Northwest. This pattern may provide a glimpse of what’s to come, according to researchers at Columbia and Cornell universities and the National Aeronautics and Space Administration (NASA). In a study published earlier this year, they predicted that a multi-decade “megadrought” stretching from the Pacific Ocean to the Central Plains could set in by mid-century, with unprecedented consequences for the regional water supply and national economy.
Drought, along with growing population and competition for resources, is driving the electric power industry’s increased focus on freshwater sustainability. Water-use restrictions in many regions are increasing pressure on thermoelectric power plants to reduce their reliance on freshwater sources. Increasingly, investors and the public are calling on electric utilities to disclose their current and future water needs.
To help plant owners and operators meet these challenges, EPRI is accelerating its research and development of advanced, water-efficient, power plant cooling technologies and freshwater alternatives in collaboration with U.S. government agencies, national laboratories, universities, electric utilities, and entrepreneurs.
Most thermoelectric power plants withdraw large volumes of water from lakes, rivers, and oceans to cool and condense steam used in generating electricity. Next-generation cooling technologies could help to conserve billions of gallons of water used by coal, natural gas, nuclear, biomass, geothermal, and solar thermal generators.
According to the U.S. Geological Survey (USGS), power plants and irrigation each accounted for about 38% of the country’s total freshwater withdrawals in 2010. The USGS reports that from 2005 to 2010, power plant cooling withdrawals decreased by 16%, due in part to a decrease in coal-fired generation, increases in natural gas and renewable generation, increased power plant efficiency, and improved cooling technologies. USGS will begin updating its estimates next year.
But water withdrawals do not tell the whole story. Because most cooling water is returned to its original source, power plants make up only 4% of freshwater consumption, according to EPRI’s analysis of U.S. Department of Energy (DOE), USGS, agricultural, and weather data. The largest consumer of freshwater in the United States is the food and agriculture sector, with a 67% share, followed by the domestic (household uses) and municipal sectors at 25%.
Broad R&D Portfolio
EPRI’s power plant cooling R&D portfolio includes nearly two dozen technologies at various stages of maturity. EPRI also is exploring options to reduce reliance on freshwater supplies by using degraded and recycled water sources (see sidebar).
“Our research on new water-cooling technologies focuses on characterizing water resources and potential breakthrough technologies, and piloting and demonstrating technologies on the pathway to commercialization,” said Robert Goldstein, EPRI senior technical executive for water and ecosystems.
Kent Zammit, EPRI manager of land and water sciences, added, “We cover a broad fleet of technologies with potential to significantly reduce plant water consumption and are developing ways to tap alternative sources for water, such as treated wastewater.”
Cooling technologies in EPRI’s research portfolio fit into three categories:
- Technologies to reduce evaporative water losses in recirculating wet-cooling systems (closed-cycle cooling)
- Technologies to improve efficiency and reduce the cost of dry-cooling systems
- Hybrid systems that combine the cost and performance of wet cooling with the water efficiency of dry cooling (see graphic)
Many technologies are being evaluated at the Water Research Center, a field laboratory at Plant Bowen in Georgia established by EPRI, Georgia Power, and Southern Research Institute.
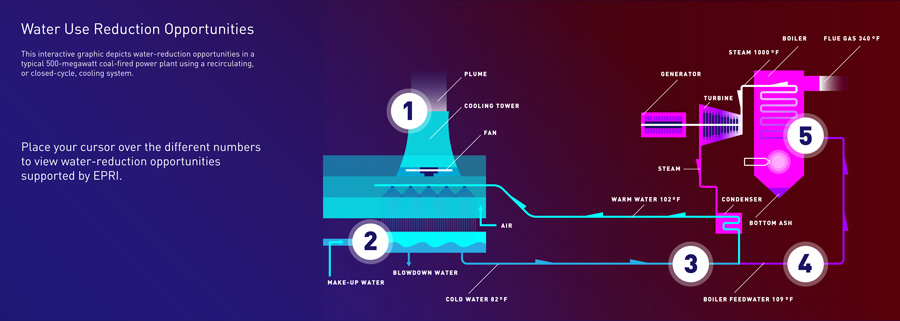
Dry-Cooling Collaborations
In 2015, DOE awarded an EPRI-led team $3 million through its Advanced Research Projects Agency-Energy (ARPA-E) to develop an economically viable indirect dry-cooling system that uses a special mesh heat exchanger with encapsulated phase-change materials. It has the potential to reduce both steam condensation temperatures and power consumption. Encapsulating the intermediate coolant also limits potential environmental problems.
EPRI and its research collaborators—including Drexel University, the University of Memphis, Evapco, WorleyParsons, and Maulbetsch Consulting—will develop, manufacture, and demonstrate a prototype by 2018.
The effort is one of five $3 million project awards from DOE’s ARPA-E Advanced Research in Dry Cooling (ARID) program. In total, DOE is funding 14 projects with a combined $30 million through ARID. This program supports technology development, from early-stage high-risk concepts to prototypes that can be scaled up for use in thermoelectric power plants, either as retrofits or new plant installations. With the program ending in 2018, commercialization could begin as early as 2020.
EPRI is participating in a second $3 million ARPA-E project led by the University of Maryland to develop a plant cooling system based on microemulsion liquid absorbents. These materials improve cooling system performance by collecting water vapor and releasing it as a liquid. The system is driven by waste heat from plant flue gas.
The DOE awards accelerate or expand research already supported by EPRI and the National Science Foundation (NSF), which last year launched a joint three-year, $6 million initiative called NSF-EPRI Power Plant Dry Cooling Science and Technology Innovation Program.
In 2014, the NSF-EPRI program selected 10 projects for funding. Of these, four target the enhancement of conventional air-cooled condensers, while six focus on developing alternative dry-cooling technologies. The latter group includes the University of Maryland–led project using microemulsion liquid absorbents—which DOE also is funding through ARPA-E—and a project with Drexel University using non-encapsulated phase-changing materials as an intermediate coolant. Compared with the encapsulated approach funded by ARPA-E, this alternative design offers potential cost advantages because it does not require a special mesh heat exchanger.
In another NSF-EPRI project, the Georgia Institute of Technology and Johns Hopkins University seek to significantly improve heat transfer and power-plant efficiency by enhancing the design of fins for the steam-condensing tubes in air-cooled condenser modules. The design’s low-cost thin reeds induce turbulence in air flowing across the fins for more efficient heat transfer and improved dry cooling. Southern Company and technology vendor SPX Cooling Technologies are supporting laboratory-scale versions, marking a path to potential commercialization.
Also funded by EPRI and NSF is a University of Illinois concept to enhance air-cooled condensers by adding aerodynamic vortex-generator arrays—devices that increase turbulence and improve heat transfer—between condenser fins.
Hybrid Systems
Separate from the ARPA-E projects and NSF-EPRI program, EPRI is funding laboratory research at the University of Stellenbosch in South Africa on the design of a hybrid dry/wet dephlegmator. A standard component of air-cooled condensers, traditional dephlegmators help condense steam and remove noncondensable gases. The University of Stellenbosch–designed hybrid system adds a new component and a second stage that enables the system to operate in dry mode when ambient temperatures are cool and in hybrid mode on hot days. This results in increased power generation, compared with conventional air-cooled condensers, and requires much less freshwater than wet-cooling systems.
According to Jeff Stallings, senior project manager at EPRI, the University of Stellenbosch is exploring two designs—a new air-cooled condenser with the hybrid dephlegmator and a retrofit version. EPRI is working with the researchers on design improvements.
The technology in EPRI’s plant-cooling R&D portfolio that is closest to commercialization, according to Zammit, is the Thermosyphon Cooler Hybrid System. Developed by Johnson Controls and demonstrated at the Water Research Center at the coal-fired Plant Bowen from August 2012 to October 2013, this hybrid system combines air cooling with an experimental cooling tower. Pending funding, a 15-megawatt thermosyphon module will begin commercial deployment later this year.
The pilot demonstration showed potential water savings from 34% to 78% on average per month. Modeling its use in the desert Southwest and other U.S. locations indicated dramatic, cost-effective water use reductions. The technology can be retrofitted in existing plants.
“EPRI is researching many different technologies that should lead to commercial alternatives to existing water conserving technologies,” said Zammit. “These technologies for new and existing plants will become more attractive, especially as water prices increase or availability decreases.”
Key EPRI Technical Experts:
Richard Breckenridge, Sean Bushart, Robert Goldstein, Jessica Shi, Jeff Stallings, Kent Zammit
If you would like to contact the technical staff for more information, send your inquiry to techexpert@eprijournal.com.
Artwork by Carl De Torres Graphic Design