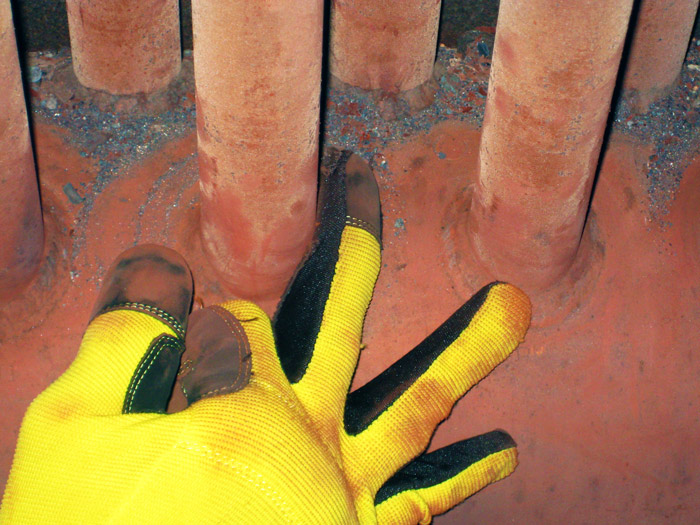
Flexible Probe Lends Hand to Crack Detection in Heat Recovery Steam Generators
During a meeting with a colleague from Southwest Research Institute (SwRI) in 2011, EPRI’s Stan Walker was trying to imagine the perfect tool for detecting cracks in the most vulnerable, hardest-to-reach nooks and crannies at power plants.
In heat recovery steam generators at combined-cycle–natural-gas plants, for instance, joints where steel tubes are welded to cylindrical headers have proven especially challenging to search for surface defects using conventional means. Many other power plant components and weld orientations with various surface geometries make it difficult to design a suitable inspection fixture.
Walker recalled how he and his colleague arrived at a solution: “I said, ‘If we could just make a tool that moves like my finger, able to move around a weld joint and maintain contact the whole time.’ And he added, ‘Now, if we can just make a flexible probe and put it on the end of your finger or glove.’”
Glove-Mounted Probe for Manual Inspections
From this brainstorm, SwRI and EPRI developed the flexible eddy current probe, which attaches to the finger of a glove and is designed specifically—and literally—for manual screening. The probe is based on printed circuit board technology using spiral metal coils embedded in a flexible substrate. The coils identify cracks using magnetic current fields.
“The probe is like a thick piece of scotch tape, not hard,” explained Walker. “At a power plant, you normally use gloves anyway, so we first placed the probe on a glove finger.”
The examiner places the finger-mounted probe on an area to be inspected, and finger pressure conforms it to the surface geometry. For example, the operator can bend his finger to inspect the circumference of a weld joint. The flexible probe connects via a small, rigid printed circuit board interface in the glove’s palm to a portable instrument that connects to a computer for viewing test results.
Typical eddy current probes are rigid, handheld devices shaped like a pencil or rectangular box. They are widely used to find defects in flat metal surfaces at power plants and in the aerospace, automotive, and chemical industries. But for weld joints and other complex geometries, such devices are often inadequate. Examinations are sometimes conducted with liquid penetrant, which can be messy in tight spaces.
Crack Detection in Field Demonstrations
Last year in field tests on heat recovery steam generators at four combined-cycle–natural-gas power plants, EPRI and SwRI demonstrated how the glove probe literally lends a hand in crack detection.
“In an examination at Southern Company’s Rowan Plant in North Carolina, we found three cracks plant staff had already discovered and one additional crack they didn’t see,” said Walker. “They wanted to know about other applications, so we demonstrated it on combustion turbine buckets, compressor blades, and the turbine rotor.”
Based on the field tests, improvements have been made ahead of the probe’s planned 2015 commercial launch. The flexible probe and printed circuit board, originally placed in a pocket sewn into the glove, are now attached with Velcro. The commercial product—which SwRI has been licensed to sell—will include all components for portable use, including a rugged tablet computer.
In addition to the glove probe, SwRI is working under contract with EPRI to interface the flexible probe with other small, portable instruments. The two companies also are evaluating designs for a robotic probe with two extendable arms to examine areas where fingers cannot reach. Called the Mechanized Over/Under Slung ET, or MOUSE, this version will travel on magnetic, motor-driven wheels along the underside of headers.
“It’s a low-cost tool, and we are still finding all these new things we can do with it,” said Walker.
EPRI Technical Expert:
Stan Walker