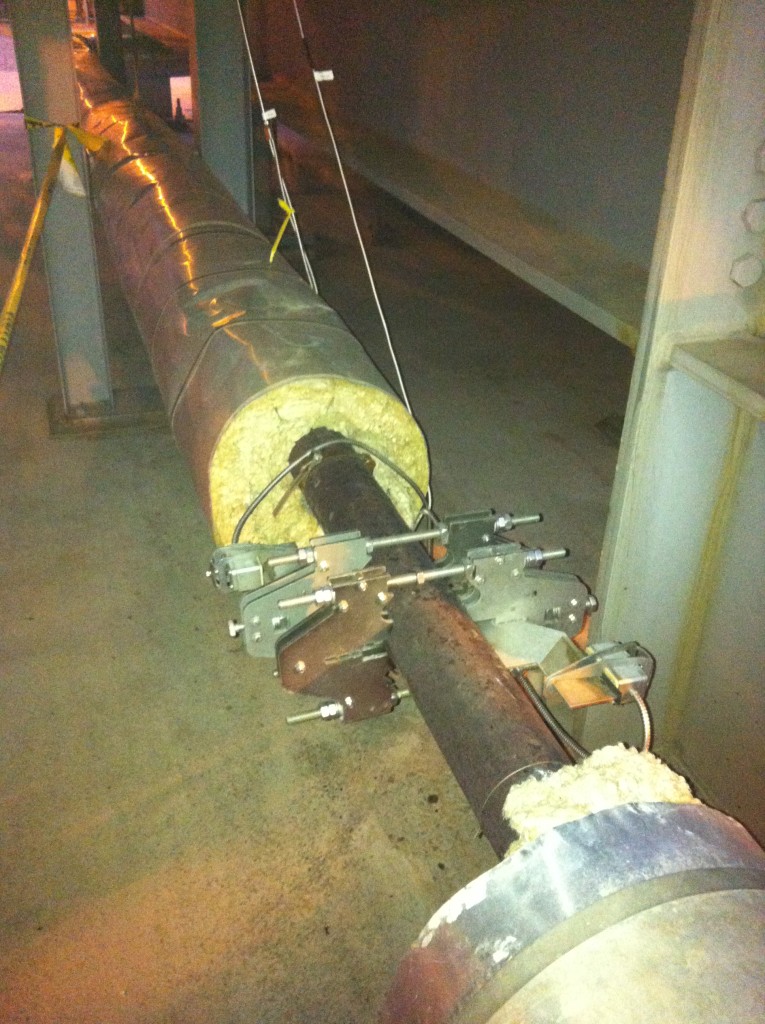
At a critical point in the post-apocalyptic movie, Dawn of the Planet of the Apes, one of Earth’s last technicians uses an ultrasonic flowmeter to measure cooling and lubricating fluids inside pipes at a hydroelectric power plant. This enables a surviving remnant of humanity to restart the plant and deliver electricity to what is left of San Francisco.
EPRI turned to the same vendor—Flexim Americas—to test a modified version of its ultrasonic flowmeter in an innovative application to detect and purge condensation in heat recovery steam generators (HRSG), preventing costly damage. Since 2010, EPRI has assessed various condensation detection alternatives and in 2012 identified the Flexim flowmeter as a promising candidate.
During power plant startup and shutdown, condensation occurs in the high-pressure superheaters and reheaters of steam generators. As designed, drain systems at many of the world’s more than 2,400 combined-cycle–natural-gas facilities do not adequately remove the condensate, which can result in severe fatigue and cracking on superheaters, reheaters, headers, and piping. It is a leading culprit in premature part failures, reduced plant availability, and increased maintenance costs. The problem is especially acute at horizontal-gas-path HRSGs, but it also can affect vertical-gas-path HRSGs.
In EPRI’s solution, the flowmeter components are attached to drain pipes. Separately installed drain valves are synchronized with the flowmeter to automatically purge the identified condensate. The system differentiates between condensation and steam by sending ultrasonic signals into the pipes and timing their return. In field trials, the Flexim equipment immediately identified water in drain pipes and clearly indicated when drain valves opened and closed.
Since 2012, EPRI has successfully installed and tested this solution at Oglethorpe Power’s Thomas A. Smith Energy Facility (a 1,250-megawatt plant in Murray County, Georgia) and at PSE&G’s Bethlehem Energy Center in Albany, New York (which has a smaller, more tightly configured HRSG) and has validated it at other plants with different drain configurations and pipe sizes. It is available to be applied to the broader industry to provide for cheaper, more reliable production of electricity.
The technology could soon replace the conventional approach for detecting and removing condensation, which involves sealing moisture in large chambers called drain pots. In a 2007 report, EPRI found that most drain pots can be ineffective and high-maintenance, whether installed with new HRSGs or as retrofits. Most HRSG operators find them too large and expensive as retrofits and typically don’t use them. This requires that drains be opened manually to purge moisture. With no way to detect moisture, operators have difficulty determining the right times to open and close drains. Closing drains too soon can severely damage pipes and headers, and opening them too often wastes energy and overuses components.
Ready for Primetime
“We are ready to go primetime in early 2016,” said EPRI Project Manager Bill Carson, adding that EPRI will assist Flexim’s rollout of the new ultrasonic flowmeter. “We have started presenting the technology to plant owners and operators. We plan to transfer this to industry next year, with commercial applications at different plants with a variety of drain configurations.”
Carson expects installation to cost less than $100,000 per plant, compared to more than $1 million for drain pots and other conventional solutions.
The two-year field demonstration at Oglethorpe Power’s unit included drain system modifications, installation of automated drain valves to purge condensate, and pressure measurements in drain pipes to confirm successful removal. “There are detailed installation and maintenance procedures, but the technology is still much cheaper than drain pots—and it is very effective at removing condensate,” said Carson.
EPRI Technical Expert:
Bill Carson