EPRI Research Supports Longer Service Lives for Spent Fuel Dry Casks
In Albert Machiels’ 33-year career at EPRI, the U.S. nuclear industry’s mandate to store spent nuclear fuel safely has extended from a task measured in years to one that will stretch for decades or more.
“In the 1970s, utilities thought they would be responsible for spent fuel for a brief time—until it was cold enough to ship somewhere else,” said Machiels, an EPRI senior technical executive who has worked on an array of research supporting safe spent fuel storage.
After four decades of shifting government mandates, utilities today face indefinite spent fuel storage at reactor sites. But nuclear plant spent fuel pools were not sized to store decades’ worth of fuel. Since the mid-1980s, operators have been moving older spent fuel from pools into dry casks, in which fuel is typically sealed inside steel canisters surrounded by concrete shielding. EPRI is leading research on managing the aging of casks, so they can continue to be licensed and used for decades, perhaps centuries.
“The good news is that industrial experience with materials used in the storage casks indicates that casks can be used for very long times,” said Machiels. “The caveat is that research has to be done to show that aging management programs will support long-term, safe storage.”
From Reprocessing to Casks: A Brief History of Spent Fuel Storage
Until the mid-1970s, spent fuel pools in nuclear plants were designed to hold fuel from one to two decades of normal operation. The U.S. government originally planned to take spent fuel and reprocess it, extracting uranium and plutonium for recycling into new fuel and disposing of wastes in underground repositories. But reprocessing was controversial because some reprocessed material can also be used in warheads. In 1977, President Jimmy Carter banned it. President Ronald Reagan rescinded the ban in 1981, but by then the civilian reprocessing program was deemed too costly.
In 1982, Congress endorsed the construction of geologic repositories for underground disposal of high-level radioactive waste, including spent fuel from nuclear power plants and military wastes. In 1987, Congress designated a repository site at Yucca Mountain, Nevada, and the U.S. Department of Energy (DOE) signed contracts with utilities to take spent fuel beginning in 1998.
Meanwhile, “operators were running out of room in their spent fuel pools,” said Machiels. They began retrofitting pools with storage racks with neutron absorbers, so more fuel assemblies could be packed into the pools without going critical. “But that still had its limits,” he said. “So in the early 1980s, EPRI research explored alternatives including moving fuel assemblies into dry cask storage systems, a technology initially developed in Germany. That technology prevailed following a highly successful joint demonstration project conducted by EPRI, DOE, and Virginia Electric Power Company.”
Supported in part by EPRI research, the U.S. Nuclear Regulatory Commission (NRC) set safety standards for licensing casks and the outdoor concrete pads where they are stored (known as independent spent fuel storage installations). By 1986, the industry began moving the oldest fuel out of pools and into dry casks. Licenses were valid for 20 years, reflecting expectations that Yucca Mountain would soon begin operations. By the late 1990s, it was clear that those licenses would have to be extended. A joint EPRI-DOE-NRC project examined fuel that had been in dry cask storage for 15 years. No evidence of degradation was found, and NRC began approving 40-year license extensions.
In 2009, the Obama administration canceled the unfinished Yucca Mountain project, and no alternative repository site has been identified. Reactor operating licenses all include a provision that radioactive wastes will be stored safely and that a repository will be available eventually. In 2012, a federal court ruled that, with the apparent demise of Yucca Mountain, NRC had to consider whether storage casks were safe for decades—well beyond 20 years, and possibly permanently. If NRC couldn’t make that finding, all reactor operating licenses were at risk. NRC studied the issue and in 2014 concluded that spent fuel could be stored safely up to 60 years in spent fuel pools, and indefinitely in dry casks, assuming that the casks were replaced once a century. NRC premised its conclusion on utilities’ implementing aging management programs to maintain cask safety.
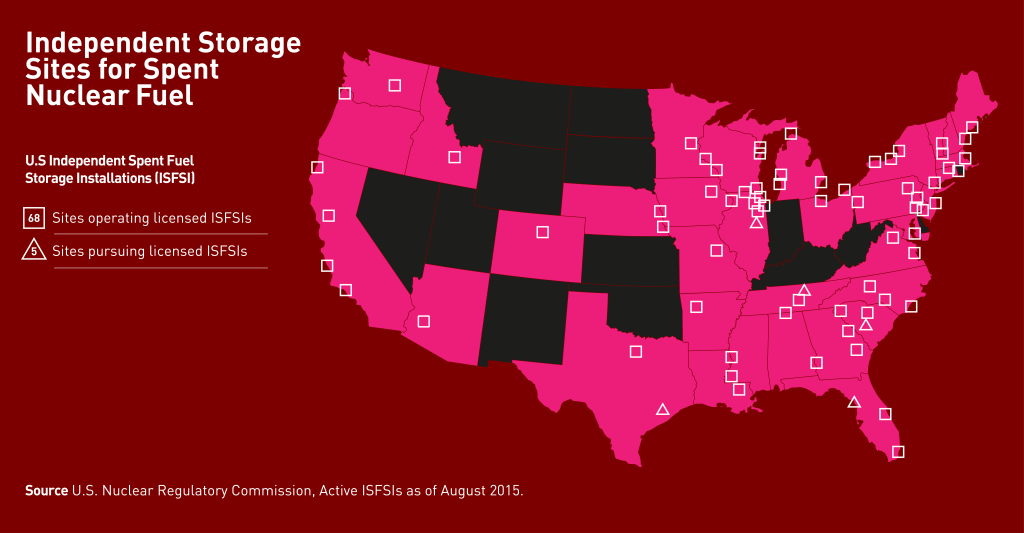
Research to Look Deeply at Aging, Including the ‘How’ and ‘Where’
For decades, EPRI has conducted research in aging management for multiple aspects of plant operations. “EPRI research has helped form the technical basis for aging management of significant reactor internal components,” said Randy Stark, EPRI’s director of Fuels, High-Level Waste, and Chemistry.
In April 2015, NRC asked the American Society of Mechanical Engineers (ASME) to develop a consensus guideline for spent fuel storage cask inspections, and EPRI agreed to support the ASME efforts. “Our charter is to identify whether degradation mechanisms exist in the stainless steel canisters, and which locations are most susceptible to these potential mechanisms,” Stark said. “Once this is understood, aging management programs for these canisters can be better developed.”
EPRI had already started examining longer-term storage safety in 2009 when it established the Extended Storage Collaboration Program with industry and government experts. “The program has grown to more than 400 members from 16 countries, all seeking to answer the same question: What needs to be done to ensure the safe, extended storage of spent fuel?” said EPRI Senior Technical Leader Keith Waldrop.
Aging management for storage casks should be far simpler than for reactors, Machiels said, because casks have no moving parts. A typical cask consists of a basket of fuel assemblies, sealed with a chemically inert gas inside a shielded stainless steel canister, which in turn is placed in a concrete overpack. Small air vents in the overpack carry off residual heat from the fuel. Casks range from about 18 feet to more than 20 feet high, have diameters of 7 to 12 feet, and can weigh more than 150 tons with fuel inside. Canisters are stored vertically or horizontally (see graphic below).
But cask inspection is not a simple matter. Casks were not designed to be inspected; at the time, operators expected a repository to open in a couple of decades, according to EPRI Program Manager Richard Reid. “They were designed to be sealed and transferred to DOE,” he said. “Getting inspection equipment inside the overpack to the canister surface is a serious technical challenge.” Heat vents can be used for access, but they measure just a few inches across. The space between the canister and the overpack is at most a few inches wide, and some designs have vertical fins that restrict movement in that space. “There is a need for not only small probes to examine the canister surface, but also small robotic devices to carry them there,” said Reid. EPRI showed progress on this front in a recent demonstration (see box at end of article).
In 2014, researchers made their first on-site inspections—including visual scans, temperature measurements, and surface samples—of two casks that had been in service more than 15 years at Exelon’s Calvert Cliffs Nuclear Power Plant, on the shore of the Chesapeake Bay. The two canisters exhibited no degradation of concern. Reid said that all EPRI research so far—at Calvert Cliffs and other field sites and from lab tests—indicates that canisters are “robust.” But he added, “There is recognition that the same materials in other nuclear plant systems are prone to degradation, and these casks will be in service a long time. We have to make sure they are well managed.” Researchers will use data now being gathered from other casks to strengthen EPRI’s cask aging models.
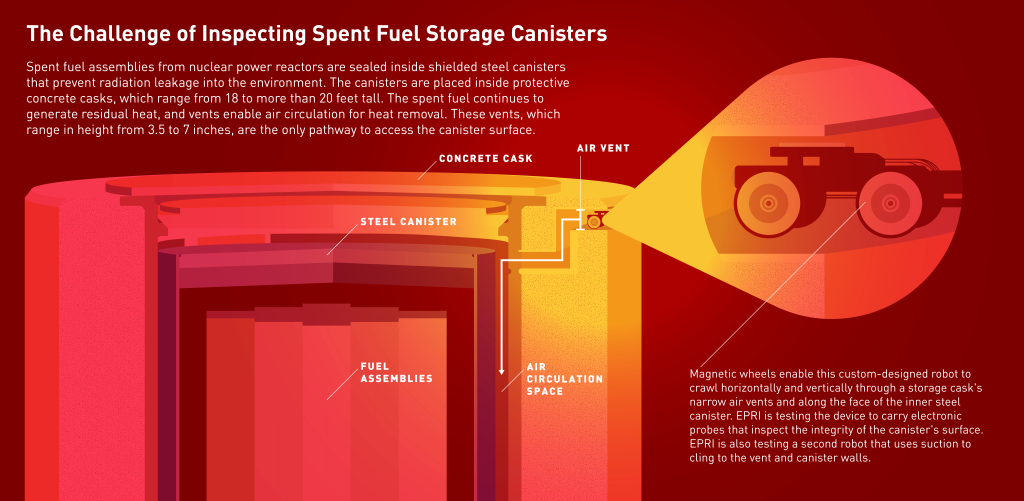
A Related Issue: Evaluating High-Burnup Fuel Storage
Over time, the nuclear industry has increased its fuel burnup to improve reactor economics. According to the NRC, the average fuel discharged from reactors today has reached the high-burnup threshold, and more of this fuel is being stored in casks. Based on laboratory research, NRC is concerned that high-burnup fuel in dry storage may have a greater potential for cracking in the zirconium alloy rod that contains the uranium fuel.
EPRI has been investigating how to store high-burnup fuel safely since the 1990s. In 2002, NRC accepted EPRI-developed technical criteria to license cask storage of high-burnup fuel for 20 years. “Many casks with high-burnup fuel are approaching 20 years now,” Machiels said. “Researchers have to confirm that the existing criteria will ensure safe storage over extended periods.”
EPRI and DOE have launched a demonstration project to confirm the behavior of high-burnup fuel during extended storage. EPRI researchers are modifying a commercial storage cask with monitoring equipment, which Waldrop called the project’s “biggest challenge.” By 2017, the cask will be loaded with several types of high-burnup fuel at Dominion’s North Anna Power Station, and key parameters including temperature will be monitored for 10 years at the plant’s cask storage facility. Rods from the cask will be tested and the results compared to those from tests prior to storage to identify any changes. “The results will enhance the technical basis for longer-term storage of high-burnup fuel,” said Waldrop.
“We know that as spent fuel cools, temperature and radiation decrease; therefore, the potential for fuel degradation is reduced as well,” said Machiels. “There will be a time when conditions are mild enough that any degradation is unlikely. We are focused on aging management to make sure that the systems protecting the spent fuel will perform properly over all the time they’re needed.”
A Little Robotic Car with a Big Mission
It resembles a toy car with outsize metal wheels. It measures 6 inches by 6 inches by 2 inches. Its headlights blink on and, with a little whizzing noise, it moves forward to the edge of a metal ledge. Then it slowly drives over the edge and straight down the wall, its magnetic wheels never losing their grip.
EPRI is testing the ability of this robotic car to wriggle its way through the narrow spaces between spent nuclear fuel storage canisters and their concrete overpacks, carrying nondestructive evaluation probes into places no human can reach. EPRI is also testing a robot that uses suction to stick to surfaces. EPRI is working with vendors to design and build both the robots and the tiny cameras and inspection probes they will transport.
In September 2015 at the Palo Verde Nuclear Generating Station in Arizona, EPRI tested the robots with an eddy current array probe and an electromagnetic-acoustic transducer probe that generated guided waves. The eddy current array probe provides more detail of the metal surface, while the guided wave probe can “see” farther and detect indications of degradation in crevices and other inaccessible areas that the probe can’t contact directly. According to EPRI Senior Technical Leader Jeremy Renshaw, EPRI research on canister and fuel aging will help determine where each probe could be most useful in detecting any degradation indications for future canister inspections.
Using full-scale mockups of two cask designs, the EPRI team demonstrated that either robot could navigate entry into the casks through available vents and maneuver in the constricted spaces inside. Both probes maintained contact with metal surfaces and recorded good data on the mockups’ surface conditions.
“We were told that this couldn’t be done, that it was impossible and we shouldn’t even try,” said Renshaw. “But both designs worked.”
Although the demonstration went well, the EPRI team identified some areas for improvement. For instance, the electromagnetic-acoustic transducer probe encountered challenges entering and exiting the cask outlet vent. “This is a minor issue that we need to address,” said Renshaw. “It illustrates how on-site demonstrations are valuable in working out the kinks in prototypes to prepare for actual field inspections.”
The storage casks now in use were designed by multiple vendors and vary somewhat in the pathways available for probe access. The EPRI team’s goal is to develop generic robots that will work with most casks and can carry various inspection tools for emerging cask inspection standards. Plans include more tests on cask mockups and, by 2018, the first-ever inspection of a canister loaded with spent fuel using probes able to detect early signs of metal degradation.
Watch a video showing the demonstration of the magnetic-wheel robot in a cask mock-up at Palo Verde Nuclear Generating Station.
Key EPRI Technical Experts:
Randy Stark, Richard Reid, Keith Waldrop, Albert Machiels, Jeremy Renshaw, Shannon Chu
For more information, contact techexpert@eprijournal.com.
Further Resources:
- Susceptibility Assessment Criteria for Chloride-Induced Stress Corrosion Cracking of Welded Stainless Steel Canisters for Dry Cask Storage Systems
- Flaw Growth and Flaw Tolerance Assessment for Dry Cask Storage Canisters
- Literature Review of Environmental Conditions and Chloride-Induced Degradation Relevant to Stainless Steel Canisters in Dry Cask Storage Systems
- Failure Modes and Effects Analysis of Welded Stainless Steel Canisters for Dry Cask Storage Systems Calvert Cliffs Stainless Steel Dry Storage Canister Inspection
- High-Burnup Dry Storage Cask Research and Development Project: Final Test Plan