EPRI Demonstrates Laser Sensors to Optimize Coal Plant Combustion
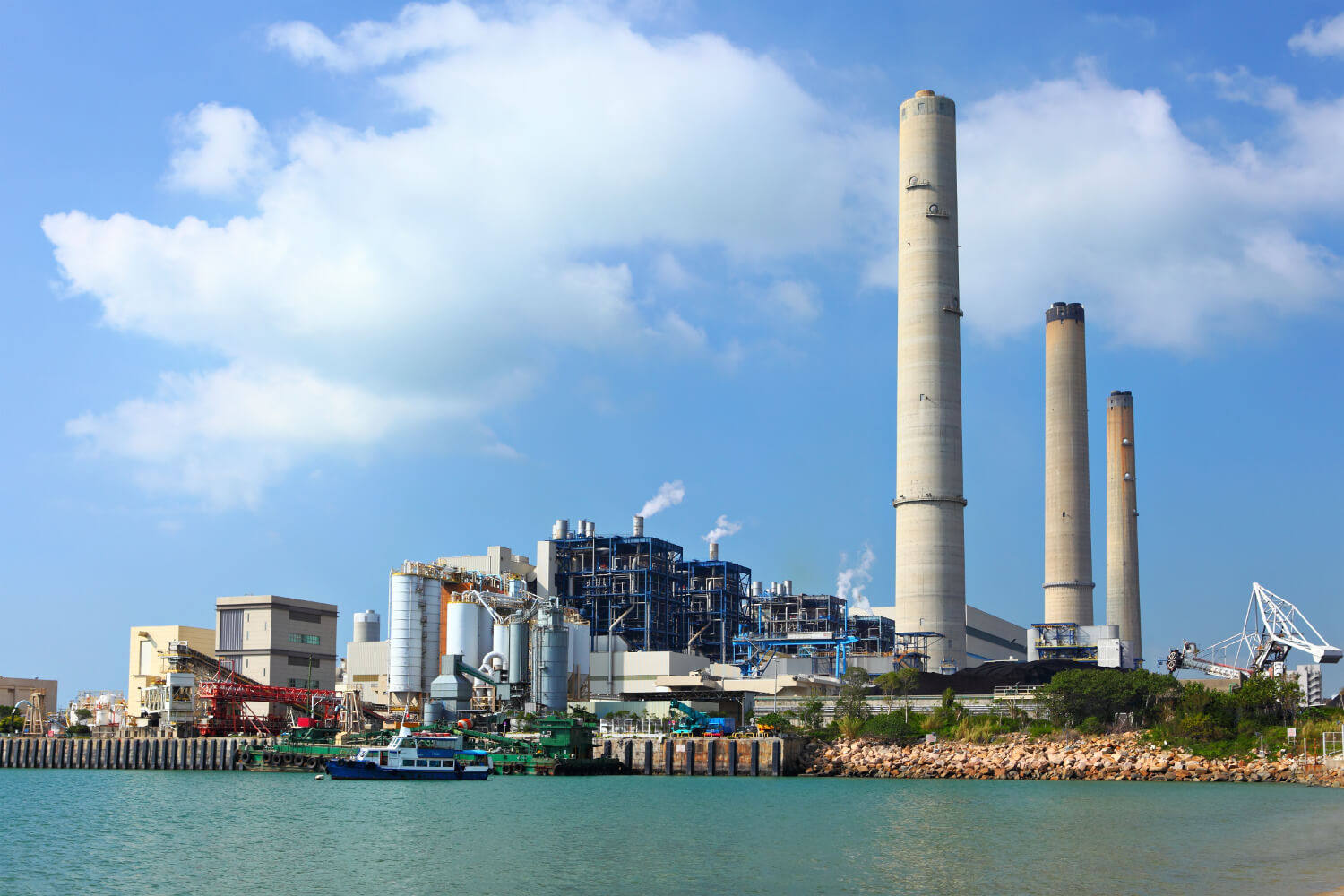
Precise measurements of combustion gases in power plants can potentially save operators hundreds of thousands of dollars each year, an EPRI study finds.
To tune boilers and optimize combustion in coal-fired power plants, plant operators periodically extract combustion gases to measure oxygen distribution, which can then be adjusted to be more uniform. Plant operators today need even more precise combustion control as they face greater competitive pressures, flexible operations, more stringent nitrogen oxide emission mandates, and the potential for carbon dioxide emission limits. This can be achieved through real-time monitoring of oxygen and carbon monoxide levels in numerous areas of the flue gas duct, which is typically 50–90 feet wide.
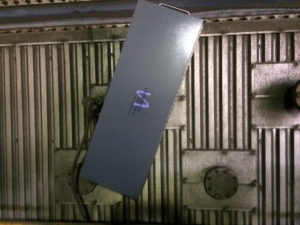
EPRI demonstrated a device that can be inserted to measure oxygen and carbon monoxide from a single point in the flue gas flow, using laser-based sensors. Over several months at an 805-megawatt coal-fired boiler, the device collected continuous measurements with high accuracy and limited maintenance needs.
While the prototype measured only at a single point, results suggest that a similar device designed for multiple-point monitoring can enable operators to fine-tune burners, reduce excess oxygen, and maintain acceptable carbon monoxide levels. This can help enhance plant efficiency and reduce CO2 and other emissions. Researchers estimate that using this approach, operators could potentially reduce annual operating costs by hundreds of thousands of dollars, based on factors such as improved boiler efficiency and reduced nitrogen oxide levels.
The study’s authors report that refinements are needed to define multi-point approaches with capital costs acceptable for commercial application. EPRI is conducting a cost-benefit analysis of potential approaches.