A report released last year by the consultancy Wood Mackenzie underlined a very specific and tangible example of how a snarled supply chain can negatively impact the electric power industry. The report found that average lead times for transformers increased from 50 weeks in 2021 to 120 weeks last year. Large substation and generator step-up transformers have lead times ranging between 80 and 210 weeks.
The impact extends to the energy supply, where wait times are up from 1-4 years to now 5-7 years for gas-fired power generation turbines combined with some markets seeing cost increases up to 2.5X.
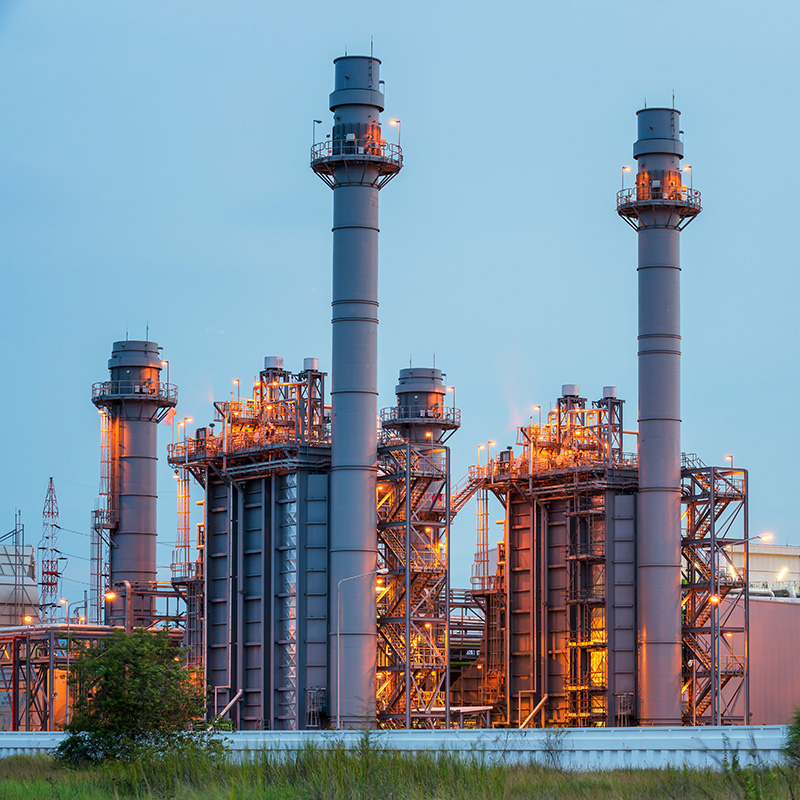
Supply chain risks, challenges, and consequences—particularly as a major contributor to inflation—have been the focus of intense analysis and debate since the COVID-19 pandemic. But what’s important to keep in mind is that the supply chain for today’s power generation equipment is well-established and includes plenty of eager buyers and suppliers.
That context is important when considering the supply chain challenges associated with a range of technologies like advanced nuclear reactors, bulk energy storage, concentrating solar power (CSP), and hydrogen production and turbines. This collection of advanced energy systems is increasingly important as the demand for electricity grows due to load growth from data centers, manufacturing, transportation, and other sectors.
Yet, for a variety of reasons, the ability to leverage these advanced energy systems is inhibited by the lack of a reliable supply chain able to produce and deliver essential equipment and components in sufficiently large quantities and in a timely manner. If anything, supply chain risks are only escalating. Tariffs, ongoing shipping bottlenecks, international conflict, global competition from other industries, and the prospect of future pandemics all underscore the risks of relying solely on sprawling transnational supply chains.
The inescapable truth is that North America and other developed nations lack the resilient local supply chains needed to mitigate these risks. One big reason is the absence of foundational manufacturing capacity to meet the demand of a rapidly growing industry. “There are a limited number of casting and forging factories,” said John Shingledecker, an EPRI principal technical executive. “We haven’t been building a lot of stuff in the Western world, so you’re constrained, or you are beholden to shipping it from overseas, which has its own risks.”
The Need for Innovative Solutions
Traditional solutions to supply chain challenges are often expensive and slow. For example, dramatically expanding forging and casting capacity in the U.S. would require billions in investment. Manufacturers are understandably leery about making large investments without plentiful orders from customers, and financial support from the government to kickstart capacity expansion is always a question mark. “It takes hundreds of millions of dollars to build a new manufacturing facility,” Shingledecker said. “Even if you want to build the biggest forges in the world, nobody is going to do that without a big market signal and usually a lot of checks.”
Building a reliable supply chain for advanced energy systems demands thinking differently. Advanced manufacturing, an umbrella term that encompasses methods such as additive manufacturing, powder-metallurgy hot isostatic pressing, and advanced welding and cladding processes, has the potential to complement existing manufacturing capacity to supply advanced energy system projects. “It’s really something that the United States is a leader in,” Shingledecker said, noting its use in the aerospace and defense industries. “There’s an opportunity for the energy industry not to replace castings and forgings but to broaden the ability to make more things quicker.”
A Collaborative Forum
Leveraging the potential of advanced manufacturing in the energy industry won’t be achieved by any single company. To kickstart the innovative thinking needed to address energy industry supply chain constraints, EPRI launched the Advanced Manufacturing Methods and Materials (AM3) initiative in 2022. A five-year effort, AM3 seeks to pursue the potential of several advanced manufacturing methods to support traditional manufacturing’s capacity to meet the demand from SMRs, bulk energy storage, and other advanced energy systems.
Since its launch, AM3 has hosted three supply chain workshops that have attracted over 120 organizations—including everyone from manufacturers to developers, utilities, and companies already pursuing advanced manufacturing—and initiated many new research and development (R&D) projects to build foundational data and skills advanced manufacturing requires and to accelerate its adoption. Research initiatives and the ecosystem of potential partners are necessarily wide-ranging because so many things need to be accomplished to begin leveraging advanced manufacturing’s capacity to deliver the materials and products advanced energy systems require.
For example, the codes and standards that have been used to guide the mass production of the materials and components of much of the power system were formulated decades ago. Evolving codes and standards to cover advanced manufacturing requires an enormous amount of collaborative data collection and testing, and it’s a necessary first step.
“The data required to change the code is often more than was originally required to implement the technology in the first place,” Shingledecker said. “But the codes and standards are critical because they are the vehicle by which you can get industry acceptance and adoption. You have to get that done, or it’s pretty much a non-starter. Suppliers need codes and standards approvals to understand what will be accepted and to drive consistency and scale across the industry.”
EPRI is leading efforts to address challenges around the acceptance of codes and standards. For instance, EPRI launched the Advanced Reactor Materials Initiative (ARMI) to develop and deploy new and existing materials for advanced non-light water reactors, and the Advanced Reactor Roadmap outlines 46 actions that are necessary to support the deployment of a future nuclear fleet.
Whether it’s innovative new reactors or other advanced energy systems, part of building a robust supply chain is qualifying materials. For instance, only six materials are qualified in ASME Section III Division 5 for high-temperature advanced reactors. Recent qualification efforts have shown that it can take up to a decade of testing and as much as $20 million to qualify a material, especially for nuclear applications and any material that will be exposed to high temperatures.
Global test campaigns are underway for some candidate materials. However, for progress to accelerate as quickly as needed, tests need to be better coordinated to produce the enormous amount of data needed to support ASME code qualification. A coordinated test program with a framework for sharing resources and accessible data will speed ASME codes and standards qualification of new materials without the need to rely on government funding, which has historically been the approach.
Incorporating Advanced Manufacturing into Demonstration Projects
Another strategy to pursue is to pair technology pilots with advanced manufacturing. Currently, pilot projects must rely on existing supply chains and materials because they must be built relatively quickly. This limits the materials and processes that can be used. “Everything they use has to be off the shelf because they’re under the gun on timeframe,” Shingledecker said. “They will use a stainless steel 316 vessel or some other traditional component that will last the lifetime of the demonstration. But they would rather use a new alloy. They also will use a casting or forging that is fine for a one-off project but will run into supply chain problems if you want to make four or five.”
An alternative approach could allow for parallel processes where components are built using both traditional forging and casting and advanced manufacturing. The lessons and data could then be used to help modernize codes and standards, which helps build a more robust supply chain.
Part of building a more reliable supply chain for advanced energy systems involves expanding the overall ecosystem of suppliers. In the UK, the Fit for Nuclear (F4N) initiative was developed by the Nuclear Advanced Manufacturing Research Centre (NAMRC) to help companies that have not supplied the industry determine their readiness to meet the high safety, operational, and quality standards. Action plans, gap analysis, and other resources are provided to help companies meet the rigorous qualifications. After the first AM3 workshop, EPRI launched a pilot F4N in the U.S. to guide companies on initial steps and highlight the need to modernize nuclear quality assurance by focusing on product quality and leveraging risk-informed programs.
TVA Embraces Additive Manufacturing
There is nothing abstract about Curt Jawdy’s experience with supply chain bottlenecks. Jawdy is senior manager of operational research and support at Tennessee Valley Authority (TVA), and his colleagues’ angst about how long it took to get components compelled him to act. “COVID really bit into the supply chain. Things that used to take three months to get now take two years,” Jawdy said. “I just got tired of listening to people stress about the supply chain, and I’m just trying to push us along the line of greater speed.”
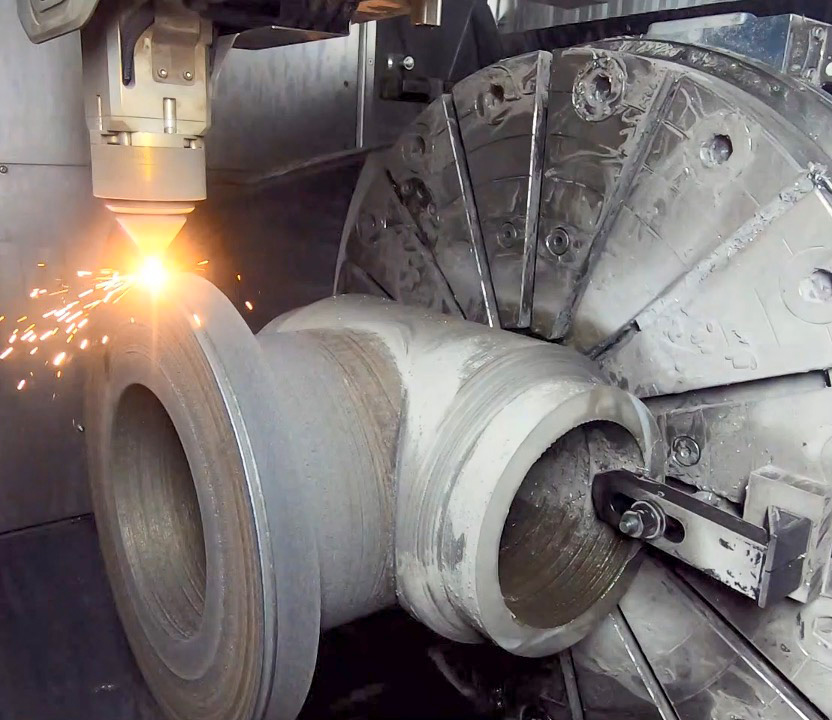
Jawdy toured the Oak Ridge National Laboratory to see the lab’s additive manufacturing research, and about a year-and-a-half ago, TV bought its first metal printer. The printer is beginning to augment TVA’s traditional machining capability, which includes one of the largest metal lathes in the nation. “We can do some very high-quality and very large machining, but where we see problems is in casting parts,” Jawdy said. “Many manufacturers have offshored casting, and that is becoming a big problem.”
Jawdy hopes that additive manufacturing can help address that challenge. TVA is still qualifying and learning more about the printer it purchased but is preparing to print some small production parts. At least initially, printing will refurbish and improve valves that the utility would previously have replaced with new valves. “You mill off the worn area, print new material, and then mill it back down,” Jawdy said. “It’s all about saving time and money because we can do these operations cost-effectively.”
TVA’s experience with its first printer has been sufficiently successful and yielded enough lessons that the utility already ordered and expects to take delivery of a much larger printer, the AML3D Arcemy X, this summer. The Arcemy X has industrial-grade welding capabilities and can print a 20,000-pound part. One of the learnings TVA will apply to its new printer is to start as early as possible on qualifying materials. “For us to meet codes, we have to do test prints and qualify those test prints with TVA welding specialists and metallurgists witnessing them,” Jawdy said. With the AML3D printer, TVA is qualifying four materials and will be sending personnel to witness test prints at AML3D’s facility in Ohio.
Once qualified and delivered, TVA plans to print a bearing housing replacement for a pump at one of its nuclear facilities. EPRI is working with TVA staff to create this part as a pathbreaker to lay down procedures, making future part printing much quicker. TVA is also hoping to use its new printer to produce a pintle, the large hinge used for doors holding back water in hydropower facilities.
Jawdy hopes other utilities will join TVA’s and EPRI’s efforts to pursue the potential of advanced manufacturing. “There are a lot of opportunities for collaboration,” he said. “No single organization can do everything, and as an industry, we need to push for speed.”
EPRI Technical Expert:
John Shingledecker
For more information, contact techexpert@eprijournal.com.