Innovative Technology Offers Elegant Solution for Disposing of Multiple Types of Waste
A process known as encapsulation is a potential game-changer for waste management at coal-fired power plants. EPRI laboratory and field studies suggest that it could safely combine disposal of two waste streams now handled separately.
The first is coal combustion products, which include fine particles of fly ash typically stored in impoundments. Recent federal regulatory actions are driving operators to close these facilities and identify alternative disposal options such as landfills.
The second is wastewater streams, such as those produced by a plant’s flue gas desulfurization systems that absorb sulfur dioxide emissions. Operators must treat such wastewater to comply with revised U.S. Environmental Protection Agency rules that include limits on dissolved solids and trace elements such as arsenic and mercury.
Technologies are available to help meet these rules. Biological technologies capture and treat selenium and convert nitrates to nitrogen. Concentrating membranes and thermal evaporation can reduce wastewater volume but produce a concentrated brine by-product for which there are few effective disposal solutions.
With encapsulation, brines are mixed with fly ash along with binders such as lime, producing a material that is transported to a landfill. This product can range from a low-moisture material with a soil-like consistency to a high-moisture, flowable paste. (Watch a video of the paste.) As the product solidifies in the landfill, its constituents stabilize chemically and physically. The solid should be resistant to rainwater infiltration, minimizing the leaching of constituents into the environment.
“The chemical reactions in encapsulation are similar to those in concrete production,” said EPRI Technical Leader Kirk Ellison. “Water and salts in the brine react chemically with fly ash, binding them as hydrate minerals and providing chemical stabilization. Solidification also occurs.”
EPRI is among the first organizations to conduct in-depth research of encapsulating power plant wastes, building on recent studies by Sasol and Southern Company. EPRI researchers are investigating the chemistry and mineralogy of the initial ingredients, the reactions, and the final products, along with the entire chain of activities: mixing materials, transporting and landfilling the product, and monitoring its long-term stability.
Decades of applying encapsulation to manage contaminated soils and mining waste provide a technical basis for its application to power plant waste management.
The Logistics of Encapsulation
Encapsulation of power plant waste streams involves five main steps (see graphic below):
- Treat wastewater to produce a brine.
- Mix the brine with fly ash and other ingredients.
- Transport the resulting product to a landfill.
- Place the product in a landfill.
- Manage the landfill.
The equipment needed for encapsulation may already be available. At the power plant, it would be necessary to deploy systems to move wastewater or brine, fly ash, and other ingredients to a mixer. Standard ash handling equipment such as pugmills could be used to combine the ingredients.
Siting the processing equipment will depend on the location of a power plant’s ash handling and moisture conditioning system. Some operators may transport the ingredients for mixing at the landfill, while others may perform initial mixing at the power plant and final mixing during transport to the landfill. Some may manage the entire process—mixing, transport, and disposal in landfills—at the power plant.
The product’s water content, determined by the mixing recipe, is an important factor during transport to and placement in the landfill. Low-moisture products could be transported by a conveyor belt or truck and placed and graded with earthwork equipment. High-moisture, flowable pastes could be pumped via pipeline into the landfill—similar to a concrete pour. Pastes can self-level without the use of landfill equipment. “Set times” for the paste to harden depend on the specific ash/brine mix and can range from a few hours to a few days.
“There will be tons of material to move,” said EPRI Senior Technical Leader Jeffery Preece. “In transporting it to a landfill, whether by land, in a paste pipeline, or on a barge, we have to understand how the material solidifies to avoid problems during transportation.”
Because coal power plants usually have much more wastewater to dispose of than ash, it would be beneficial to maximize wastewater elimination. EPRI’s research has focused on evaluating the high-moisture paste rather than the drier material because the former could potentially double the amount of wastewater a plant could eliminate.
By integrating wastewater brine and fly ash in a single waste stream, encapsulation could replace traditional ash transportation and landfilling. Disposal of pastes and other encapsulation products produces less dust than traditional ash disposal, reducing concerns about particulates in the air.
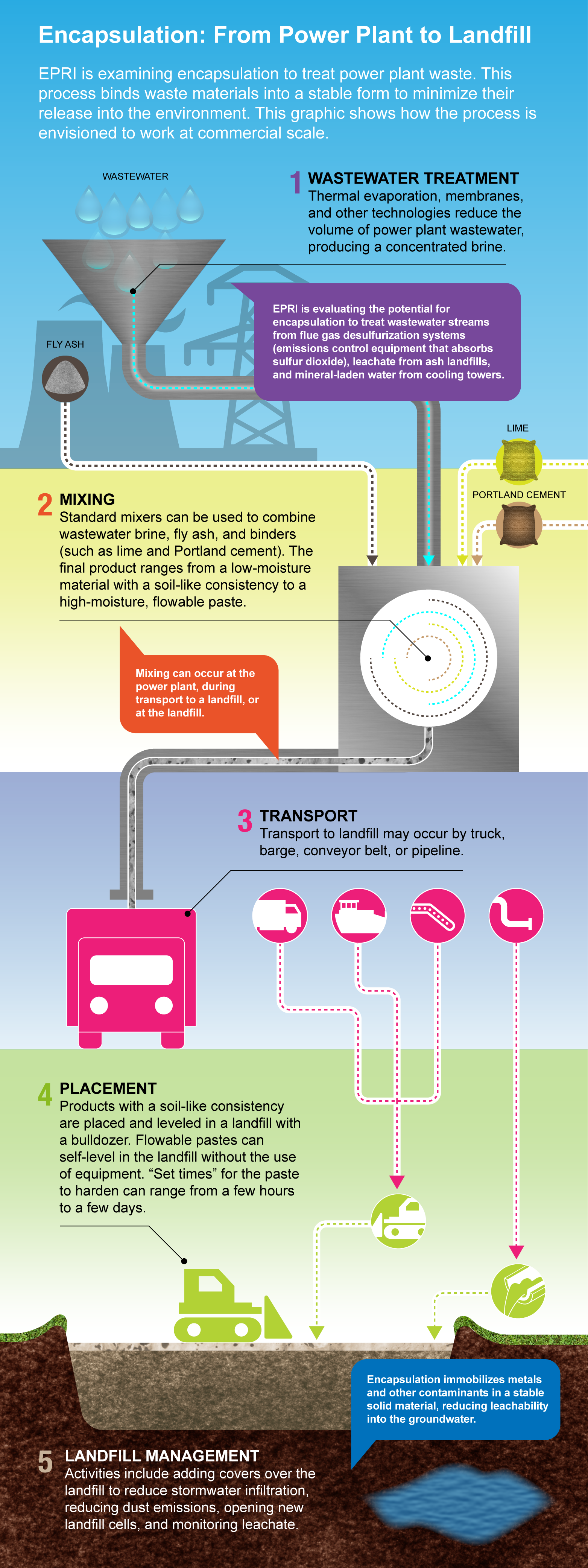
Diving into the Encapsulation Details
EPRI has completed a year of laboratory and field studies to help characterize and refine the encapsulation process.
In the laboratory, researchers investigated the chemistry of brine from treated flue gas desulfurization wastewater, which varies by coal type. For example, coal from the eastern United States produces wastewater with high salt content and reactive fly ash, while Powder River Basin coals yield wastewater with relatively less concentrated salts and more reactive ash. EPRI evaluated different mix recipes, the reactions among ingredients, and the final products’ chemical and physical properties.
“We’re compiling a first-of-its-kind database with information about the various materials that form from these chemical reactions,” said Preece.
Field studies in 2016 looked at four different wastewater chemistries at two coal plants, including flue gas desulfurization wastewater, blowdown, and leachate from an on-site ash landfill.
At the Water Research Center at Southern Company subsidiary Georgia Power’s Plant Bowen, a pilot encapsulation system mixed wastewater with fly ash, lime, and other binding materials to produce a chemically and physically stable paste. EPRI and Southern Company compiled data on the mixing process, the chemical reactions, and the differences among brine chemistries. They examined various aspects of landfill management, such as placing the paste, adding covers for stormwater runoff, reducing dust emissions, and determining when to open new landfill cells.
“We developed recipes and figured out how to move the product to a disposal facility,” said Southern Company Senior Engineer Benjamin Gallagher. “We found that mixtures could be pumped and placed effectively, demonstrating that the technology is ready for full-scale testing. By testing chemically and physically diverse materials, we covered the gamut of conditions across our fleet and found that we can encapsulate wastewater from any of our plants.”
Encapsulation may not be cost-effective at plants where wastewater volume is very large relative to the volume of ash, because wastewater volume reduction systems can be capital- and energy-intensive.
“Encapsulation is the leading option for several of our power plants because it saves capital investment costs compared to wastewater treatment systems—and the final product has favorable environmental properties,” said Gallagher. “There’s no wastewater to discharge, which helps us streamline compliance with wastewater permits.”
Expanding the Field Tests, Fine-Tuning the Processes
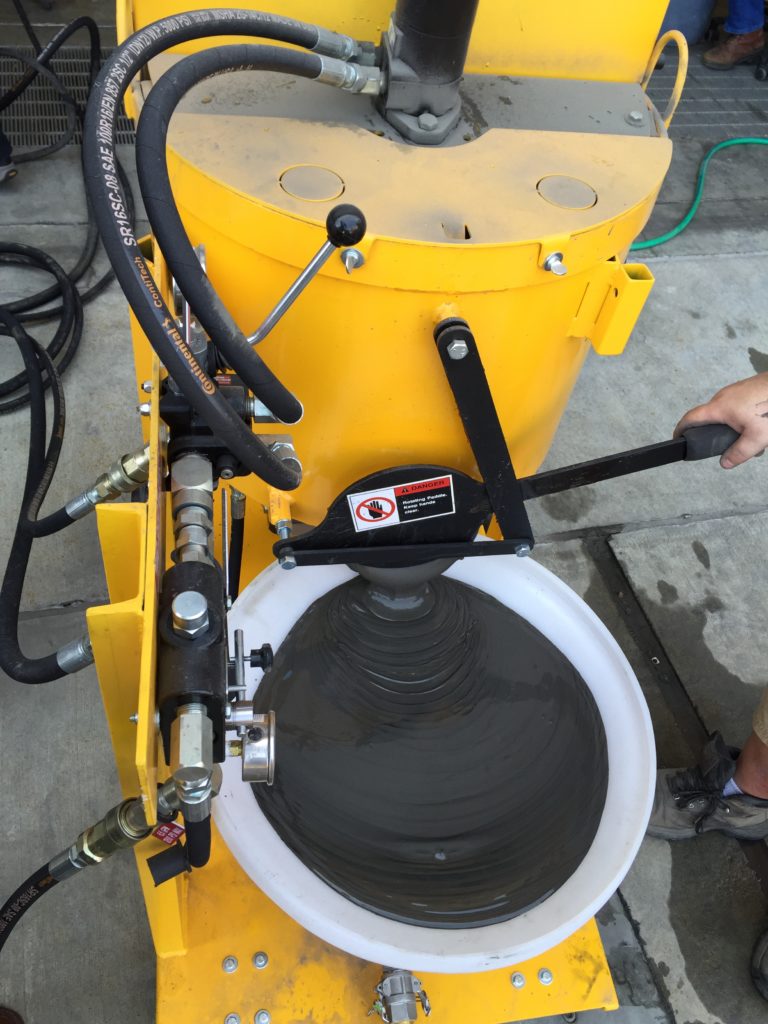
While encapsulation shows promise as a reliable waste management technology, the biggest question is determining where it is technically feasible and cost-effective. In 2017 and 2018, laboratory and field testing will expand to six flue gas desulfurization wastewater chemistries covering most coal types in the United States.
“At a range of sites, we’re going to field-test a pilot encapsulation system with an off-the-shelf grout mixer, along with different evaporative technologies for making wastewater brines,” said Ellison. “We plan to establish test landfill cells, fill them with encapsulated material, and monitor runoff and leaching for one to two years.”
EPRI will continue to optimize brine chemistries and encapsulation recipes that yield impermeable products, and will evaluate the various costs—capital investment, equipment operations and maintenance, and materials transportation. EPRI will investigate applying encapsulation to difficult-to-treat wastewater streams such as those from carbon capture and storage, which can be three times saltier than ocean water.
“Could encapsulation be used at any power plant and for other types of wastewater? As we get more answers about the chemical reactions and the properties of the products, we’ll be able to answer that more clearly,” said Preece.
“Developing a cost-effective, reliable technology that effectively eliminates the discharge of wastewater at power plants would be a great win for the energy industry,” said Southern Company’s Generating Fleet R&D Manager Jeff Wilson. “The results of encapsulation testing at the Water Research Center show that this technology has a promising future.”
Key EPRI Technical Experts:
Kirk Ellison, Jeffery Preece
For more information, contact techexpert@eprijournal.com.