Ontario Power Generation Advances Efforts to Wirelessly Monitor its Nuclear Power Fleet
The Story In Brief
“You need to have people at the right level of the organization who can build that vision, continue to foster it, and help other people see it as well,” says Kathleen Carew, Acting Vice President, Fleet Operations, Maintenance and Radiation Safety at Ontario Power Generation (OPG). Carew spoke with EPRI Journal about OPG’s nuclear plant modernization initiative and instilling a culture of innovation among its staff.
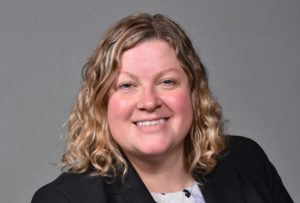
EPRI Journal: Why is OPG modernizing its nuclear fleet? How do OPG’s nuclear plant modernization efforts fit into the company’s decarbonization goals?
Kathleen Carew: OPG recently announced a goal to be net-zero carbon by 2040, and nuclear plant modernization will play an important role in achieving this goal. At our Darlington nuclear plant, there are two parts to our modernization efforts. First, because the plant was originally licensed to operate until the early 2020s, we have a large refurbishment underway to extend its life until about 2055. The refurbishment includes disassembling and rebuilding large infrastructure such as the reactor core. We completed unit 2 earlier this year, and we’re now finished defueling unit 3 and well into the disassembly phase of the project. We expect the entire refurbishment to be complete by 2026.
Second, and in concert with the refurbishment, we are creating more effective ways to monitor plant equipment to enable better decisions and more efficient plant operations. This is not only at Darlington but also at our Pickering nuclear plant and other generation facilities across the company. With better monitoring, we can do condition-based maintenance, which reduces the number of maintenance hours. That means operators need to spend less time going to the field to collect information. If these processes can be automated, our employees can spend more time on other work such as testing safety systems.
EJ: Describe the monitoring technologies deployed.
Carew: We have installed the wireless infrastructure—including 900-Megahertz gateways—that serve as the backbone of our monitoring efforts. We deployed 50 wireless temperature sensors at Darlington and another eight at Pickering. These measure temperature in rooms with equipment such as electric switchgear. They’re intended to inform insights about aging of components and repair decisions.
We are also deploying wireless and wired sensors on components to continuously monitor their conditions. They monitor parameters such as vibration, temperature, and humidity. Sensors on batteries and motors measure voltage and current. You can tell if a pump motor is in distress by gathering this data for motor current signature analysis and electrical signature analysis. This can enable us to make decisions on pump replacements especially for the ones that aren’t accessible when the plant is online. Some of these sensors are already installed while others are planned.
Our wireless networks have improved radiation monitoring. Previously at Darlington, whole body monitors were wired into the local communication network. Now, wirelessly connected whole body monitors enable technicians to respond to events more quickly. We plan to configure wireless radiation monitors to transmit real-time radiation data to workers’ mobile devices, which can help with job planning.
We have established our Monitoring and Diagnostics (M&D) Center, located near the Pickering plant. Staff at the center use advanced pattern recognition and other machine learning tools to analyze data from wireless sensors deployed at Pickering and Darlington. This helps them to identify trends and anomalies and determine when components may need to be replaced. Some algorithms automatically send alarms to our staff when potential problems are found. So far, condition-based maintenance has reduced about 2,600 maintenance hours annually, saving about a million dollars.
We are piloting additional software that can detect anomalies in more plant systems. While software takes care of numerical data analysis, the expertise of the M&D Center staff is crucial to turning this analysis into good decisions. We have merged the M&D Center with OPG’s Data Analytics Department, providing the center with access to more staff expertise in machine learning techniques. To make fleet operations more efficient, we’re connecting and integrating datasets from departments across the company, including financial, health and safety, asset management, and generation. We’re planning an initiative to use natural language processing to analyze plant condition records for trends.
Considering how quickly artificial intelligence, data integration, data visualization, and robotics technologies are advancing, I would expect a day in the life of the M&D Center to look a lot different five years from now. The center’s evolution is driven not only by technology development, but by our creativity and imagination in envisioning new solutions.
EJ: What other modernization technologies have you implemented?
Carew: We’ve set up virtual tours for employees, using 360-degree images similar to what you see on Google Street View. You can virtually walk through the entire plant as if you were on Street View. There are many applications. One example is that there’s a plant tour we typically give staff for radiation protection training and qualification. Now, we’re able to now do that tour remotely, which saves time and resources and allows trainees to complete the tour at their own pace. Plant staff can also use the virtual tours to plan for maintenance or other tasks, which can help reduce the amount of time they spend in radiologically sensitive areas. They can assess details that aren’t in engineering drawings, such as clearances and the layout of equipment. They can answer questions such as, “How far off the ground is that valve? Am I going to need a ladder?”
EJ: What lessons or recommendations might you share with other nuclear plant operators who are earlier in their modernization process?
Carew: It’s important to define an organizational vision so that you don’t end up with competing priorities. As you implement new technologies, make sure that you maintain executive sponsorship in your company because the technologies’ benefits may not be initially clear. You need to have people at the right level of the organization who can build that vision, continue to foster it, and help other people see it as well.
Changing or updating processes is necessary sometimes. If you use a new technology with old processes, you may not realize the full benefit of the technology. It’s about constantly reviewing how you do business and asking, “Now that I have implemented this new technology, is this process still appropriate?” As a plant implements new automated monitoring technologies, it can stop performing the manual activities that were in place before. For example, after temperature sensors are deployed in certain rooms, a plant operator can eliminate a technician’s daily temperature readings in those rooms.
At the same time, because you are installing equipment at a nuclear plant, you need to be patient and take the time to follow the governance in place for modifying your facility. Modernization is a journey.
EJ: Historically, the nuclear power industry has been risk-averse and conservative about making changes. Yet, a willingness to try new approaches and a culture of innovation are needed for plant modernization to succeed. How are you instilling these cultural changes among OPG’s nuclear plant staff without compromising safety?
Carew: We foster an innovation culture by encouraging staff to propose their new ideas on an online forum. Internal committees evaluate suggestions and provide feedback to the authors. At both Darlington and Pickering, we established collaborative innovation initiatives that empower staff to brainstorm on problems that need to be solved, find commercially available products that can be used to solve these problems, and develop new technologies. We have innovation labs with software and equipment such as 3D printers and soldering stations that staff can use to design, build, and evaluate new devices. These efforts have allowed the development of numerous products that are now deployed in our plants, including a wireless battery monitoring system and wireless equipment sensors that measure vibration, acceleration, humidity, temperature, and ambient light.
We developed temperature monitoring sensors and software that are used for COVID screening of OPG employees. Early in the pandemic, temperature sensors were scarce, and some were inaccurate. Our staff determined that when the outside air is cold, the skin temperature of people coming into the building can be quite cool. We decided to develop our own technology which includes a device that accounts for ambient temperature.
Innovation also happens in pilot projects where we can test new concepts and technologies in a safe environment before scaling up for deployment across the fleet.
EJ: How have EPRI’s plant modernization initiative and tools helped OPG with its modernization efforts?
Carew: An EPRI guide on implementing plant monitoring programs formed the basis of our M&D Center. We also use various EPRI guides to optimize the deployment of wireless sensors on plant equipment such as vertical pumps, generators, and horizontal pumps.
It’s also helpful being part of EPRI’s forums and hearing from others in the industry who are modernizing their plants. When thinking about new technologies and processes, sometimes there is a tendency to say, “We can’t do that because… insert technical reason.” But then I would go to an EPRI meeting and hear people say, “We do that. We have a Monitoring and Diagnostics Center. We monitor all our plants from one remote location.” I really enjoy hearing about—and sharing with my team—the innovations being used across the industry, and my participation adds value to OPG and the many innovative work programs we have underway.
Photos of Pickering Nuclear Generating Station and Kathleen Carew courtesy of Ontario Power Generation.