And why solar modules toxicity testing matters to utilities and the solar industry’s reputation
Although the forecasts vary, there is little doubt that solar will provide an increasingly large percentage of the electricity used around the world. According to the research and consultancy group Wood Mackenzie, solar accounted for 46% of all new U.S. electricity generating capacity added in 2021. In its Solar Futures Study issued last year, the U.S. Department of Energy laid out a roadmap for solar to produce at least 37% of America’s electricity by 2035—up from around 3% today.
Regardless of the exact proportion of electricity provided by solar, it’s clear that the volume of solar modules that will need to be recycled or disposed of in the future will increase dramatically. According to a report produced by the International Renewable Energy Agency and the International Energy Agency’s Photovoltaic Power Systems Program, the cumulative volume of waste photovoltaic (PV) modules globally could reach 1.7 million metric tons by 2030 and over 60 million metric tons by 2050—an amount that would represent about 10% of current e-waste volumes.
Given the rapidly accelerating growth of solar installations, the fact that PV modules typically have a 20- to 30-year lifespan, and the accumulation by some owners of modules experiencing early failures, it’s important for plant owners and utilities to rapidly develop science-based approaches to manage PV modules that have reached the end of their useful life. One important reason to do this is that failure to develop transparent and environmentally responsible methods for handling large volumes of PV modules threatens the reputation of clean energy.
“All technologies have benefits and challenges. The fact that there can be trace amounts of toxic elements in PV modules, even if small in mass, is something that needs to be dealt with,” said Stephanie Shaw, a technical executive at EPRI whose research focuses on assessing and reducing the environmental and health impacts of energy generation and storage. “There is an inaccurate narrative that says that PV is not environmentally friendly because we are swapping the harm of fossil fuels for the harm of toxic or critical materials. But there are already options to recycle and reuse those materials before they need to be disposed. We need to improve those options, make them more cost-effective, and incorporate them into the normal environmental management processes for all types of solar PV projects.”
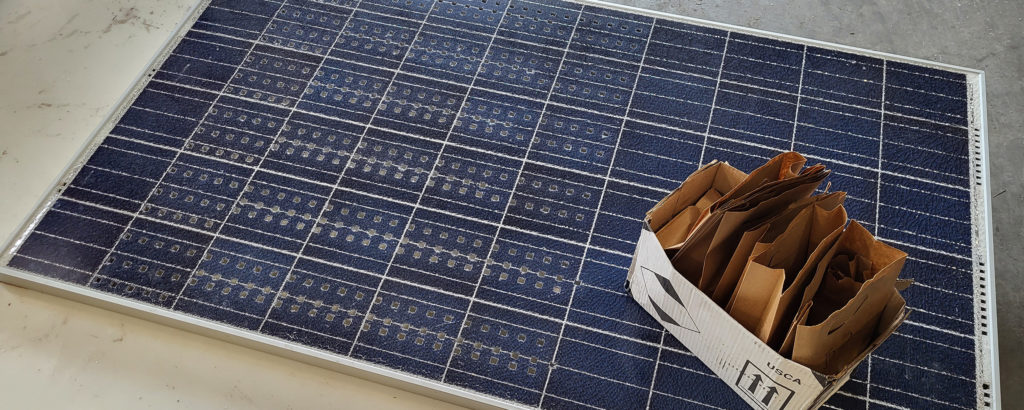
A New Standard for Sampling PV Modules
The recent release of an ASTM International standard practice represents an important step forward in providing a uniform and science-based approach to classifying solar modules for disposal. The practice is based on a standard operating procedure developed in EPRI projects, including Assessing Variability in Toxicity Testing of Photovoltaic Modules. More recently, EPRI and a number of utility and solar industry partners have collaborated on the supplemental project Improving PV Sampling Methods for End-of-Life Leach Testing. EPRI and the Photovoltaic Reliability Laboratory at Arizona State University (ASU) also presented PV Module Toxicity Methods and Results: A Literature Review at IEEE’s 2022 Photovoltaic Specialists Conference (PVSC).
Co-led by Shaw and EPRI principal technical leader Cara Libby, this ongoing research began with the understanding that many PV modules contain hazardous materials, such as lead and cadmium. Both materials have the potential to leach into ground and surface water if they are not classified properly before being recycled or disposed of in a landfill.
Currently, PV modules in the United States have to pass the Toxicity Characteristic Leaching Procedure Test (TCLP) to be disposed of in a non-hazardous landfill. Modules that don’t pass the TCLP are deemed hazardous waste and must be disposed of following far more stringent and expensive processes.
In the past, however, no uniform approach for extracting samples to be sent to TCLP labs existed. “EPA [Environmental Protection Agency] Method 1311 is the methodology used to determine how much material leaches out of an object ,” Libby said. “Besides defining the maximum size and weight of the sample to be tested, it doesn’t tell you how to obtain that sample. So, you could take a drill or a saw or a hammer to cut pieces from the module laminate, include pieces of the aluminum frame or the electronics, or send the entire module to the TCLP lab and let them figure it out.”
The result is that a sample from a crystalline silicon module could comprise only material with no lead, like pieces of aluminum frame and cell areas with little metallization. Using such a sample, a TCLP lab would deem the module non-hazardous. But another sample from the very same module—say, from the solar cell interconnect ribbon areas, where there typically are significant amounts of lead—could be designated as hazardous. “We said, ‘There has to be a way to do this more consistently to avoid biasing the results,’” Libby said.
Finding Ways to Reduce Variability
Working with ASU and other partners, EPRI began developing a standard sampling protocol by first understanding why test results vary so much and then examining ways to improve their consistency. As a start, EPRI and its partners worked with ASU to send identical samples to a number of testing labs to see how much the results varied. Results were repeatable within the labs, but they were not replicable between different labs without clear and consistent instructions to not crush the samples further.
In the effort to reduce the variability in test results, researchers first used a diamond bit drill to extract samples from the module laminate. They learned that mechanical cutting methods could not achieve reasonable variability. “We saw huge variations, including the same module either passing or failing, depending on the sample extraction method,” Libby said.
Instead of a drill, saw, or grinder, a water jet that shoots water at a very high force was used to cut samples from the modules. The improved precision of the water jet further reduced test variability because the pieces were less fragmented and cracked.
Perhaps the most important step in improving the consistency of test results was to preclude use of samples that are biased in terms of where they are collected within the module laminate. To do that, ASU came up with an approach that is now part of the ASTM standard. Samples include a total of about 100 grams of material from all four key sections of a module: the cell area, the cell ribbon area, the string ribbon area, and the non-cell and non-ribbon area.
The amount that comes from each area is proportional to that area’s relative size and weight in the overall module. “ASU has a calculation so that proportional numbers of pieces from each of the key sections of the module represent the mass distribution in a real module,” Shaw said. “Most of the sample is the cell.”
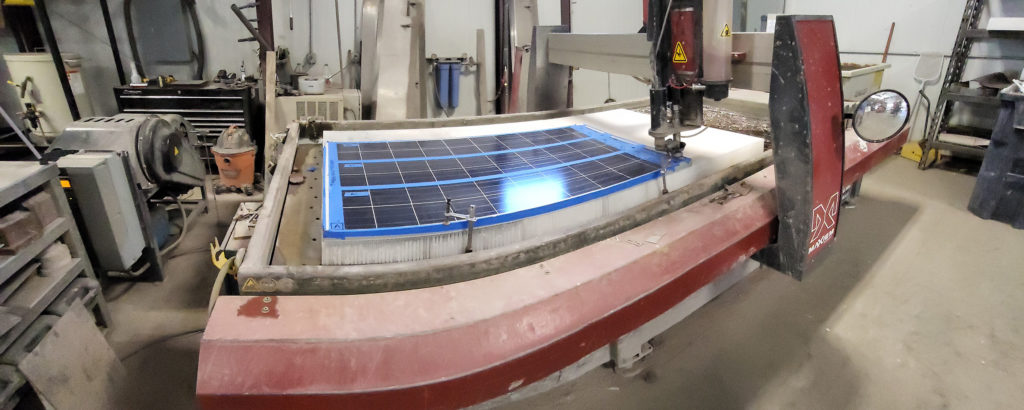
Delivering Consistency and Confidence
One potential benefit of the ASTM standard is its incorporation into procurement requirements when utilities source modules for solar installations. Facility owners already ask manufacturers for results of leach testing; now they can request use of the ASTM standard in collecting samples for the testing.
Consistent sampling can also lower risks and provide significant financial benefits at the end of a module’s life. In the United States, responsibility for module end-of-life management typically rests with the PV plant owner. The plant can send a module to a water jet lab to extract samples, which are then sent to a TCLP lab.
Given the costs of classifying a module as hazardous or non-hazardous, it’s important to be certain that test results are precise. “If you put in the effort to get a sample, you want to make sure you can trust the results,” Shaw said. “If you improperly classify a large volume of modules as non-hazardous based on inaccurate tests, you could face fines or have to retrieve modules from landfills. Or you could spend a lot of money treating them as hazardous when they actually aren’t.” Besides offering potential financial benefits and risk mitigation, the standard helps utilities achieve their environmental stewardship objectives.
For ConEd, a funder of the research that ultimately led to the standard practice, there are potential benefits for both its regulated and its non-regulated businesses. ConEd’s Clean Energy Businesses owns and operates solar power plants across the country.
Most of ConEd’s solar projects are early in their life cycle, and any modules that need to be taken out of operation are recycled. But John Oldi, manager of environmental programs for Clean Energy Businesses, says now is the time to establish processes and standards to consistently and transparently recycle or dispose of a large volume of solar modules at the end of their useful life. “From a regulatory and larger sustainability point of view, understanding the composition and risks associated with modules as a waste stream is important for me from an operational standpoint,” Oldi said.
More specifically, Oldi said, ConEd could develop a protocol for sampling modules using the ASTM standard. Having a consistent approach to sampling modules for toxicity testing is also important to William Slade, project specialist for ConEd’s Environment, Health and Safety division. “Waste management is the number one place of risk for the company’s reputation and liabilities,” Slade said. “Making sure we have the right answers about characterizing waste is important.”
Another potential benefit of the research that led to the ASTM standard is to inform any potential state regulations about the disposal of modules. In a state like New York, this is particularly important. “New York is committed to a huge build-out of modules and farms, and research shows there is a big bump of waste as the modules reach the end of their lives,” Slade said. “We hope we can provide good data to help if rules about disposal are developed so that regulations are workable and make sense for the industry.”
EPRI’s work in this area will continue. One area of focus is creation of a database of TCLP results from a variety of manufacturers and module types to help identify whether there are common characteristics that lead to a pass or fail determination.
Other questions require additional investigation and testing. For example, little is known about how weathering from environmental impacts like ultraviolet light exposure, temperature changes, and wind could change the leaching behavior of a module over time. “A plant owner might require a manufacturer to provide TCLP results at the beginning of a project,” Libby said. “But 30 years later, when the modules are taken out of service, will the results still hold? We want to make sure cracks, backsheet tears, and corrosion from moisture ingress don’t affect TCLP results. That is something we are hoping to test this year.”
EPRI Technical Experts:
Cara Libby, Stephanie Shaw