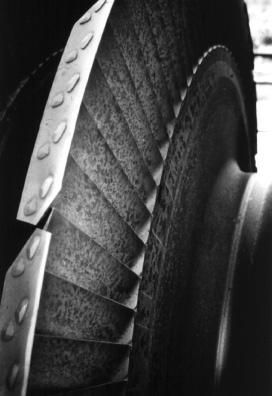
During power plant shutdown and layup modes, steam turbines are exposed to oxygen, and the resulting corrosion can form tiny pits on turbine blades at random locations. Over years of operation, these pits can act as initiation sites for cracks that can destroy one or more blades or even entire turbines. In worst-case scenarios, such damage can force generation units out of service.
Significant knowledge of corrosion-related risks has been compiled through decades of operational experience and research on turbine pitting and cracking. Yet until recently there has been no way to help predict the life expectancy of blades with pitting.
Since 2010, EPRI has led an international team of experts—including the UK’s National Physical Laboratory, Austria’s University of Natural Resources, and U.S.-based SimuTech Group—to develop the industry’s first methodology for such predictions. EPRI’s Technology Innovation Program funded the effort.
“While significant research has been undertaken on preventing corrosion damage and crack growth, we focused on crack initiation—when a pit morphs into a crack—because there has been very little work on this,” said EPRI Technical Executive David Gandy. “The key question we were trying to answer was, when an operator discovers a turbine blade with pitting, how much life does it have left?”
Plotting Pits and Cracks
At the University of Natural Resources in Vienna, Austria, the research team conducted ultrasonic fatigue tests on turbine blade specimens with artificially generated pits and cracks. Using a special test chamber, the team accelerated the corrosion process so that it took less than 14 hours for the specimens to reach the end of their useful life. Compared to traditional field testing, this enabled researchers to more quickly compile and process data on how the material weakened. The tests allowed the team to understand the relationship between corrosion pits and subsequent cracking on two common types of steel blades when subjected to various operational conditions and stresses.
“These tests enabled a rapid assessment of fatigue damage,” said Gandy. “Performing standard fatigue tests in a corrosive environment can take up to a year or longer. We were able to do our testing in less than a week in most cases.”
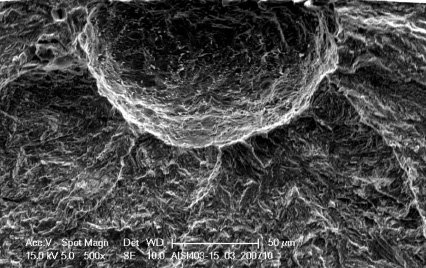
Plotting pit size against the stress level reveals a definitive line indicating safe operation. “The research showed that if you are below the line, where pits and the stresses are small, then blade failure is not a concern,” said Gandy. “But above the line, the blade is in a more risky condition.”
Applying to Industry
Using the test results, the researchers devised a methodology that operators can use to help predict when blades are at risk of fatigue failure, given a specific size of corrosion pit. Key steps are:
- Inspecting blades for pitting by measuring and documenting the location of deep pits
- Calculating stresses
- Correlating stresses with the location of specific pits and diagramming the results
- Determining an appropriate safety margin for continued operation
- Scheduling blade replacements in advance
The team demonstrated the methodology on a 600-megawatt fossil-fuel turbine with pitted blades, predicting the risk of continued operation under different operating scenarios.
EPRI incorporated the methodology into a beta-version spreadsheet that operators can use to predict blade failure. In 2015, EPRI plans to expand this spreadsheet into a software program.
EPRI Technical Experts:
David Gandy, Steve Hesler