We Energies Reduces Disposal Risk with ASHphalt
When Bruce Ramme joined We Energies in 1980, he didn’t expect his University of Wisconsin–Milwaukee master’s thesis on fly ash use in concrete to be of much use in his transmission and substation engineering job. Yet Ramme encountered a compelling reason to continue thinking about fly ash, a mineral by-product produced when coal is burned at a power plant. “When I came here, I found that only five percent of our fly ash was being used,” said Ramme, now vice president of We Energies Environment Group.
Now, 35 years later, We Energies uses nearly 100% of its fly ash and other coal combustion products (see chart), including gypsum and bottom ash. According to the American Coal Ash Association, the U.S. electric power industry’s average use rate is approximately 45%. Recycling coal plant gypsum materials for wallboard and agricultural products generates revenue for We Energies and minimizes risks and expenses associated with landfill disposal. “Strict Wisconsin regulations make landfilling very expensive and helped motivate us to find better uses for these materials,” said Ramme.
Turning Fly Ash into ASHphalt
For years Ramme pondered the use of fly ash in asphalt for road pavement but was stymied by the response from manufacturers. “They always told me, ‘We have our own filler,’” he said.
Dissatisfied with their answer, Ramme returned to his alma mater, the University of Wisconsin–Milwaukee, to learn more. A professor directed him to a paper by a Turkish researcher concluding that fly ash has a positive impact on asphalt. “The study found that fly ash reduces the need for bitumen oils that help asphalt ingredients stick together,” said Ramme. “It also is much more cost-effective than bitumen oils and results in less cracking.”
To test these findings, We Energies funded a 2005 study at the University of Wisconsin–Milwaukee. The utility created a technical advisory panel with representatives from a county highway department, the Wisconsin Department of Transportation, civil engineers, and university researchers. Ken Ladwig, an EPRI expert on coal combustion products, was brought in to help guide research design and to review the results. “The study demonstrated fly ash’s potential benefits for asphalt durability and longer life—all at a lower cost,” said Ramme.
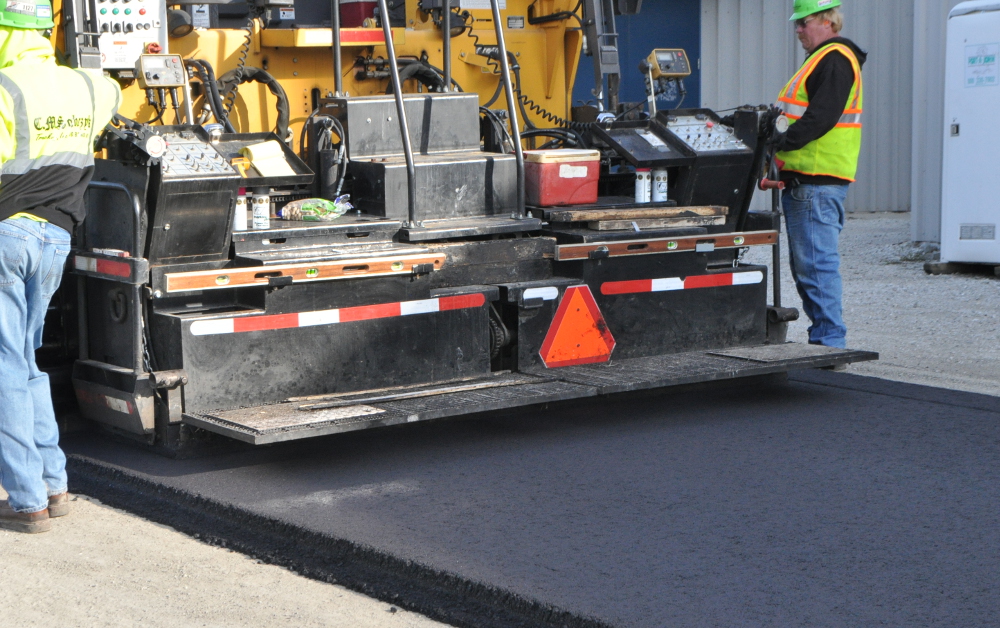
We Energies continued to work with academics and EPRI to develop and test a product called ASHphalt—a form of asphalt that uses fly ash to bind its ingredients. In 2012, We Energies and the University of Wisconsin–Milwaukee investigated ASHphalt’s performance in a road pavement project at the utility’s Oak Creek coal plant. The demonstration project confirmed what the utility had discovered in its earlier study with the university: A road paved with ASHphalt can be cheaper and more durable than one paved with traditional asphalt.
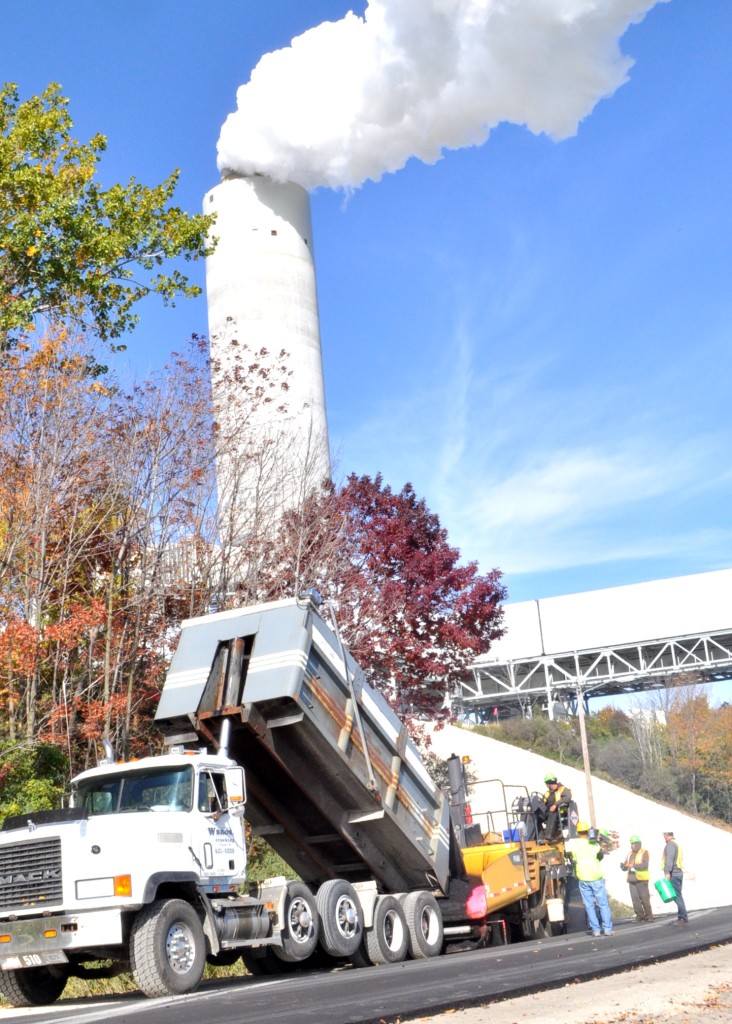
According to Ramme, EPRI’s involvement in each R&D step was essential. “We don’t have dedicated researchers in our company,” he said. “The EPRI experts helped us more fully tap our in-house talent to develop and implement rigorous, defendable research needed for wider application and success.” Ramme also credited an EPRI research project, supported by We Energies and other utilities, that facilitated laboratory tests and demonstration projects on the durability of fly ash–based binders.
The Road Ahead: Paved with ASHphalt
In addition to producing better performing asphalt at a lower cost, other benefits of using coal ash for asphalt include reducing the amount of ash sent to landfills and creating a more environmentally sustainable approach for repairing and rebuilding roadway infrastructure.
EPRI is involved with We Energies’ continuing ASHphalt testing at other facilities. As with its other beneficial uses of coal combustion products, We Energies recognizes that commercializing and developing a market for ASHphalt can give the utility and its customers an economic boost. “If you can take materials with a disposal cost and turn them into products with revenue, that’s a big benefit for customers and the general public,” said Ramme. “There’s huge savings in not throwing things away and making use of these valuable mineral resources.”